The desire to have integrated and working parts that allied together to maintain a facility led to the establishment of maintenance software.
These “paperless” systems were designed to help facility managers lessen the stress of needing to put the information on paper.
The drawback to this, it didn’t work – many computerized maintenance software systems reduce only a modest amount of paperwork because they are so cumbersome to use.
We find many facilities that receive written work orders from both internal staff and external vendors.
Not only do these systems continue to rely on paper, but they also create more hassle and confusion for busy people like you.
Counterproductive, right?
Are you still scheduling and assigning daily maintenance tasks to technicians and staff with paperwork orders and activity checklists?
Are they then marking off the paperwork after each task and giving it back to you for review?
We have a term for this: nonsensical.
Oh wait, and then it goes into a filing bin where it sits for days, sometimes weeks.
This can’t go on…Save us.
Please save us all!
Old, Problematic Systems
Activities then go overlooked, or your maintenance items end up getting skipped until the asset becomes a significant liability.
Your labor costs then become only a smidgeon of the expenses amassed by your facility once faulty equipment runs undetected.
This can be avoided with easy-to-use maintenance software.
We’ve seen some complex software, and we’re sure you have too.
Many systems are old-fashioned and problematic for facility managers (like yourself) and staff to learn.
Effective use of these systems usually requires extensive on-going, like forever, training.
Who’s got time for that?
There’s no flexibility, and the need for paperwork when implementing the software still exists!
When you’re working your-you-know-what-off to put maintenance protocols in place, who has time for a little more salt on the wound?
Not you!
The systems many managers use are, quite frankly, a burden.
That is something no one has time for, especially you.
Archaic software systems and the need for paperwork were the problems associated with original, outdated solutions we see available.
We figured you’d want to remove the use of paper from your maintenance system entirely.
We also figured you’d want to combine it with the automation of all facility maintenance tasks.
Did we figure correct?
We’re talking work orders, purchase orders, and preventive maintenance–paperless and automated! Yes.
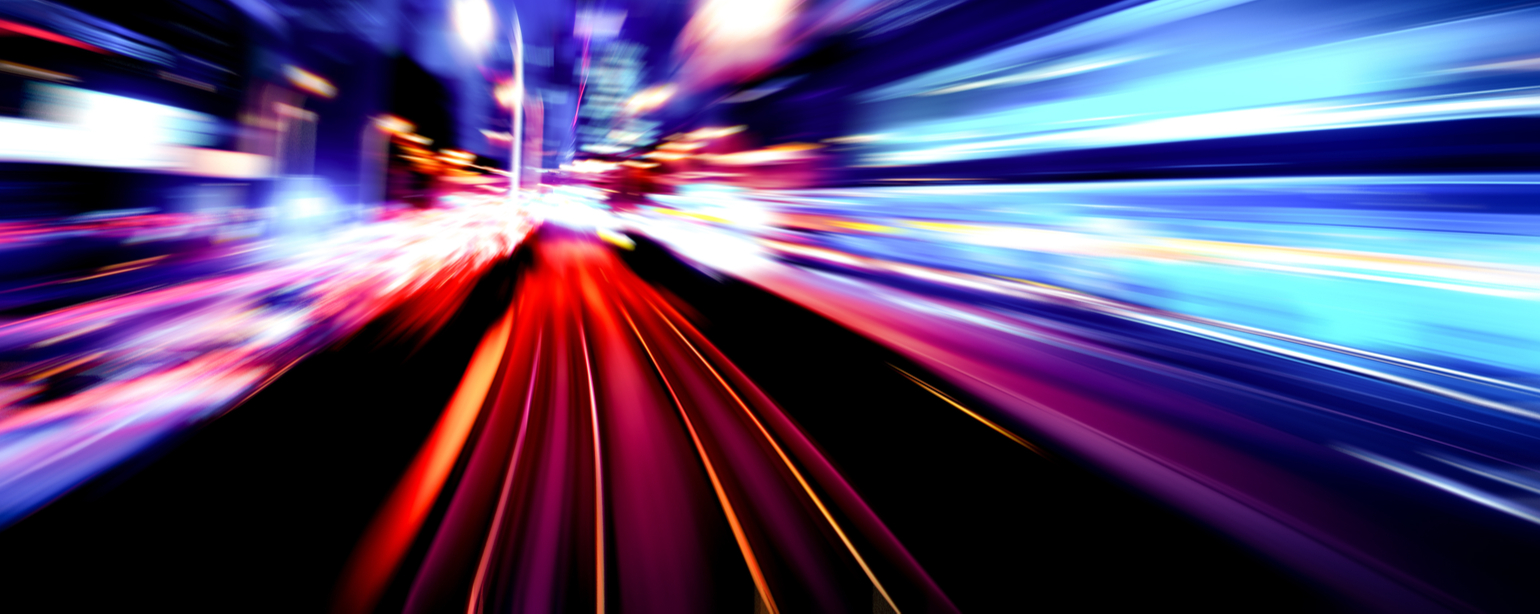
Say Bye to Paperwork and Your Work Order Woes
Maintenance systems have evolved into functionally progressive systems.
They provide facility managers, engineers, and technicians with the functionality and tools needed not only to maintain their facility maintenance but to improve all associated processes during implementation.
Yes, these do exist.
These are the type of systems that give you that value over time you need.
Did you ever think a time would come when you’d say maintenance system and ROI in the same sentence?
The time has come.
A valuable system will also be a web-based solution.
You know, one that can be accessed via the internet from anywhere, anytime.
It’ll also help organize your system to your facility’s needs.
Incredible, these solutions do exist.
Setting them up is a breeze.
A super easy-to-use system will let you organize and enter departments, locations, activities, equipment, material, tasks, vendors, documents, purchase orders–need a quick breath–requests, work orders, priorities, and forms – all from the comfort of your office, and to your liking.
Customize as you like.
It’s your software – in high gear.
An intuitive system, well, that’s the dream.
Using a system that will maximize the potential of your facility maintenance operations should always be a goal.
Removing difficulty starts with using a system that gives you the ability to manage it effortlessly.
Setup should be a trouble-free process, leaving you and your staff with an operational system for immediate use, where your work orders, purchase orders, and preventive maintenance activities can be executed.
The keyword here is ‘execute.’
Vendors, equipment, and materials should be entered directly into the software for each facility, with little or no stress.
A robust system will similarly give you the power to document comprehensive details for each type.
All inter-reliant pieces of the maintenance system will bring you loads of value if they’re all connected throughout your solution.
Then, you’ll know you’ve got something here worth the investment.
Want an example?
We thought you’d never ask.
Let’s say that a maintenance supervisor receives a work order request from someone in Housekeeping logging a toilet with broken pipes.
Yes, the one causing a flood in a high traffic public restroom in the middle of a busy day!
The supervisor can instantly add the work order details to the system.
Directly from the details screen of the work order, all the pertinent information can be added without moving to ancillary windows.
Now, this is the type of maintenance solution we want!
It’s not déjà vu; your dreams are coming true.
While tracking the general details of the work order within a great system, you get a timeline of the work order from when it was scheduled to its completion.
The chain of command, requesting department, who the work order will be assigned to, any associated labor, equipment, materials, and attachments can be added to the work order details from one screen.
Preventive maintenance tasks can be entered for the work order directly from the screen.
You read right; there are systems where you can create and execute maintenance tasks based on activities without headaches.
(It’s time we move our acetaminophen to the bottom desk drawer.)
Your staff can all be ‘Employee of the Month’ with new-age maintenance solutions.
How?
Here are four ways for you:
- An activity to conduct a quarterly filter change on an air handler can be scheduled in the system with associated tasks.
- Tasks for this activity might include checking the drip pan, clear the drain, check for leaks, and replace the filter.
- The activity can be scheduled for a specific time and date each quarter.
- All associated equipment, materials, and labor also can be included in the activity details.
What would bring a maintenance system into high gear?
Reporting and – you guessed it – analytics.
Nowadays, there are solutions with reporting features, providing you with access to various reports and summaries to assess performance.
Reports can range from a breakdown of all your work orders and purchase orders active in the system, preventive maintenance, activities, equipment, vendor work orders, and purchase orders, to labor-related information.
Yes, it gets better.
Some of these systems let you manipulate your reports as needed and export them to a spreadsheet.
Turning Your Maintenance Software into High Gear
How does the functionality of a maintenance solution generate value over time for a facility?
What’s the individual realized return on investment for you, the facility manager?
These are only a couple of the questions you could be asking when choosing your maintenance system.
(For more, check out our blog on choosing a CMMS. It’ll give you the nine questions we believe you need to be answered ‘Yes.’)
Here’s some immense value a useful, reliable, and starkly excellent maintenance solution will bring to your facility.
The system will allow your managers – no questions asked – to easily create, track, edit, and automatically communicate work orders, including creating web forms, allowing users to send in works orders for approval.
Set your team up for success with the ability to set up a chain of command approval for work orders based on the type and amount.
A chain of command will have different approval levels giving you a way to put protocols in place for how work orders are granted.
Now you’re in control.
What a relief, right?
Some systems will let you set each level of the chain with specified requirements for authorizing an approval.
We know preventive maintenance can be a scary word, whether you’re on the collegiate or professional level.
Not anymore.
Your preventive maintenance tracking can be possible in a calendar format, allowing you to easily view and make changes, including a drag and drop option for changing dates.
The type of solution you’re looking for will let you see everything in daily, weekly or monthly formats.
Let’s top that.
Creating checklists gives you complete control and consistency of asset maintenance.
This ensures warranted checks that do not go overlooked – all bases are covered.
Stress…relieved.
A solution with fixed asset and material inventory tracking gives you a logical way of being alerted so you never, ever run out of what you need.
Automatic notifications can be sent when inventory falls below your reorder amount.
It’s the natural progression of things, and now your operation is running, naturally.
Automated notification reminders can alert staff when vendor insurance and warranties are expiring.
In a system with extra value, you can also set alerts and notifications preventing an interruption with business activities.
Talk about hitting the cruise control button on your maintenance system!
Don’t stop there.
Supplement cruise control with full access to a multitude of purposeful and intricate reporting features.
You and your team are only as good as the information you can manage.
Then, the solution with the utmost value will give you comprehensive one-click reports, charts, and graphs to provide you with an accurate breakdown of work orders, preventative maintenance, fixed assets, materials, and vendor information.
See the information the way you need to see it.
Statistics give you all the data you need to increase your operational efficiency.
This is where control and efficiency can be measured because you know where your resources are being allocated.
Over to You
We gave you the key.
We started the ignition.
It’s up to you to put your maintenance initiatives into high gear and set it to cruise control.
Editor’s note: This post was originally published in September 2014 and has been updated for comprehensiveness and freshness.